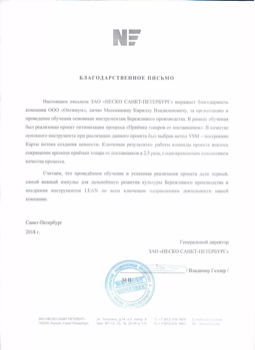
ZAO «NESCO ST.PETERSBURG»
By this letter, CJSC NESCO ST. PETERSBURG expresses its gratitude to Optimum LLC, personally to Kirill Vladilenovich Mesenyashin, for organizing and conducting training on the basic tools of Lean manufacturing. As part of the training, a project was implemented to optimize the process of "Acceptance of goods from suppliers". The VSM method was chosen as the main tool for the implementation of this project - building a Value stream Map. The key results of the project team's work were a reduction in the time of acceptance of goods from suppliers by 2.5 times, while simultaneously improving the quality of the process.
We believe that the training and successful implementation of the project provided the first and most important impetus for the further development of the culture of Lean manufacturing and the introduction of LEAN tools in all key areas of our company's activities.